An information guide for business and property owners to inspect their commercial roof.
Note: All do-it-yourself maintenance guidance outlined is to be completed under safe operating conditions. If fall protection is not available, it is best to hire a licensed contractor.
1
Roof covers
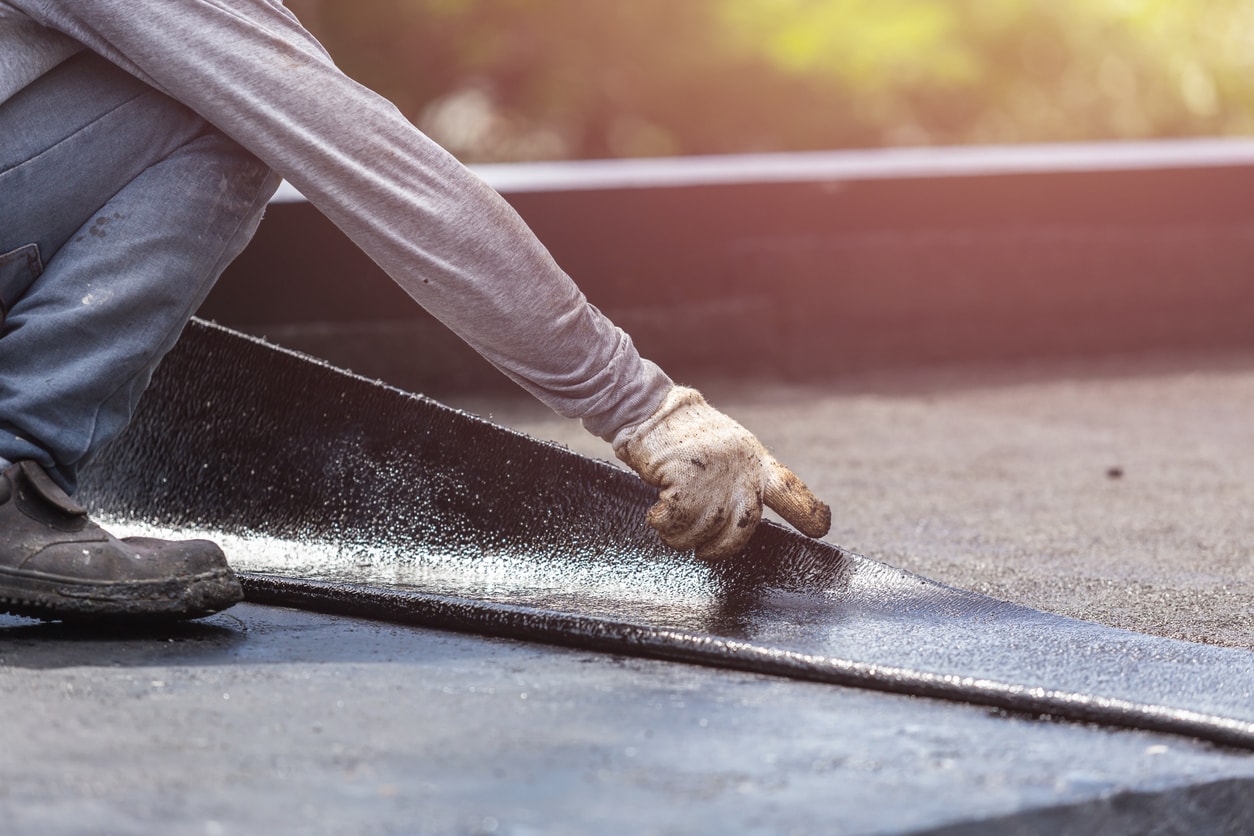
Low–slope/flat roof cover
For all low-slope/flat roof types, long-term standing water can cause excessive weathering, allowing your roof membrane to become brittle. Signs of long-term standing water are mold and vegetation growth. Check the underside of the roof or on your drop ceiling to see if there are any signs of water damage, which is a sign of damage to your roof cover system. Other aspects to consider include:
- Ballasted roof system: Inspect for uneven distribution of rocks. If there are bare spots, move the rocks back evenly into place, covering all exposed roof membrane. Be careful not to damage the roof membrane.
- Built-up and modified bitumen: Monitor the cover for bubbles/blisters, cracks, excessive wear around connections, tears, punctures, and excessive weathering resulting in loss of embedded gravel or smooth surface protective coatings for built–up roofs.
- Single-ply: Inspect and repair tears, worn seams, seam failure, gaps, fasteners backing out, punctures, and brittleness. For adhered or glued-down systems, inspect for excessively loose membranes and blisters.
- Sprayed polyurethane foam: Monitor for excessive weathering, tears, or punctures, which causes a loss of the acrylic coating.
- Metal panels: Inspect for loose screws and deteriorated rubber washers, which can wear down over time. Inspect for discolored or worn off paint, which acts as an anti-rust layer, and for signs of rusting. Additionally, look for dents or divots.
Steep–slope roof cover
Verify that the roof is holding its shape and not bowing. Other aspects to consider include:
- Asphalt shingles: Inspect for curling, loose, and/or torn shingles.
- Clay and concrete tiles: Inspect for cracked, missing, or unattached tiles.
- Metal panels: Inspect for loose screws and deteriorated rubber washers, which can wear down over time. Inspect for discolored or worn off paint, which acts as an anti-rust layer, and for signs of rusting. Additionally, look for dents or divots.
2
Roof drainage systems
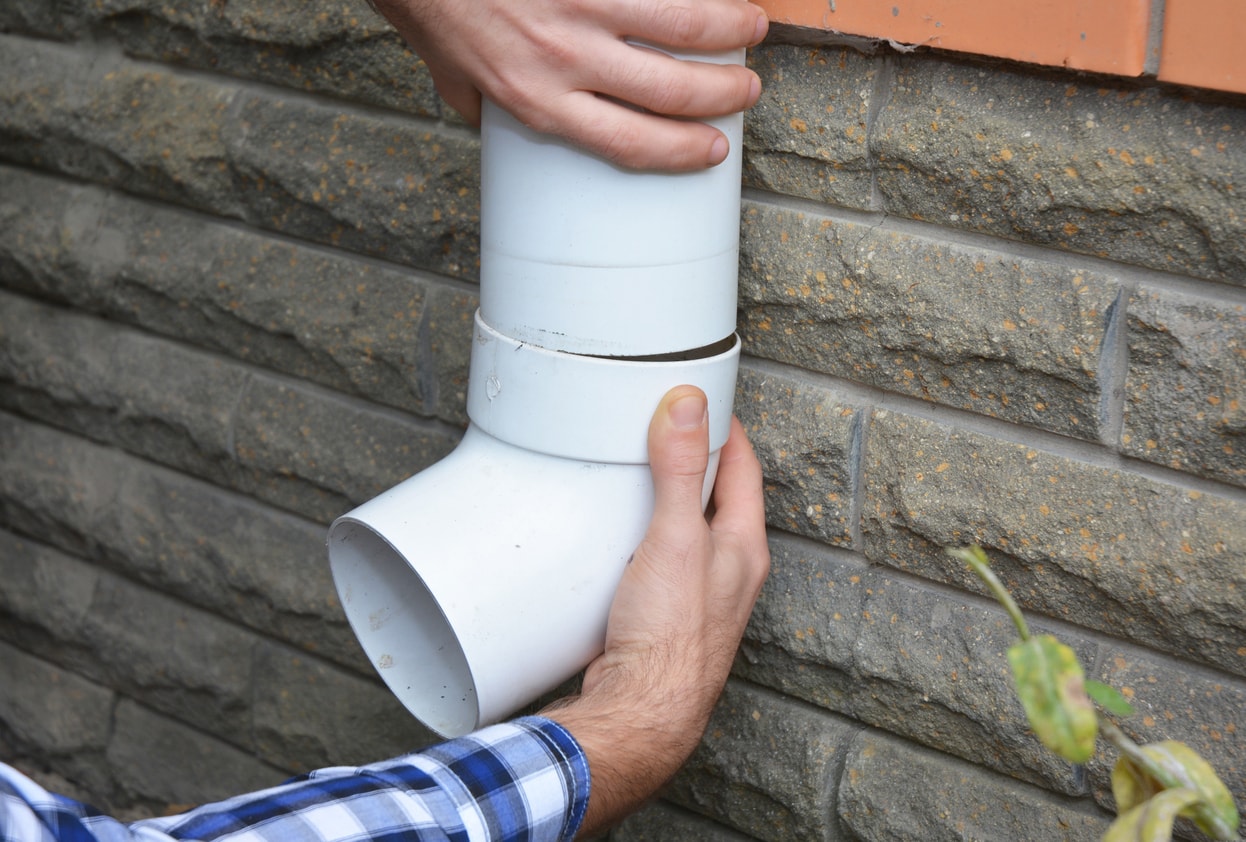
- Remove loose objects like leaves, sticks, and construction debris from your roof as well as dirt and other granules from interior roof drains, gutters and downspouts, which can cause blockage during a storm.
- Check for long-term standing water in gutters and correct any blockages that may be the cause. If there are no blockages but standing water still occurs, ensure gutter is properly sloped to the downspout.
- Verify that gutters are anchored by gutter straps designed to resist the high winds associated with hurricanes and other severe storms.
- Inspect for missing or loose sections of the gutter system, particularly near the downspout.
3
Metal roof edge flashing (the strip of metal installed around the roof edge where the roof cover meets the wall)
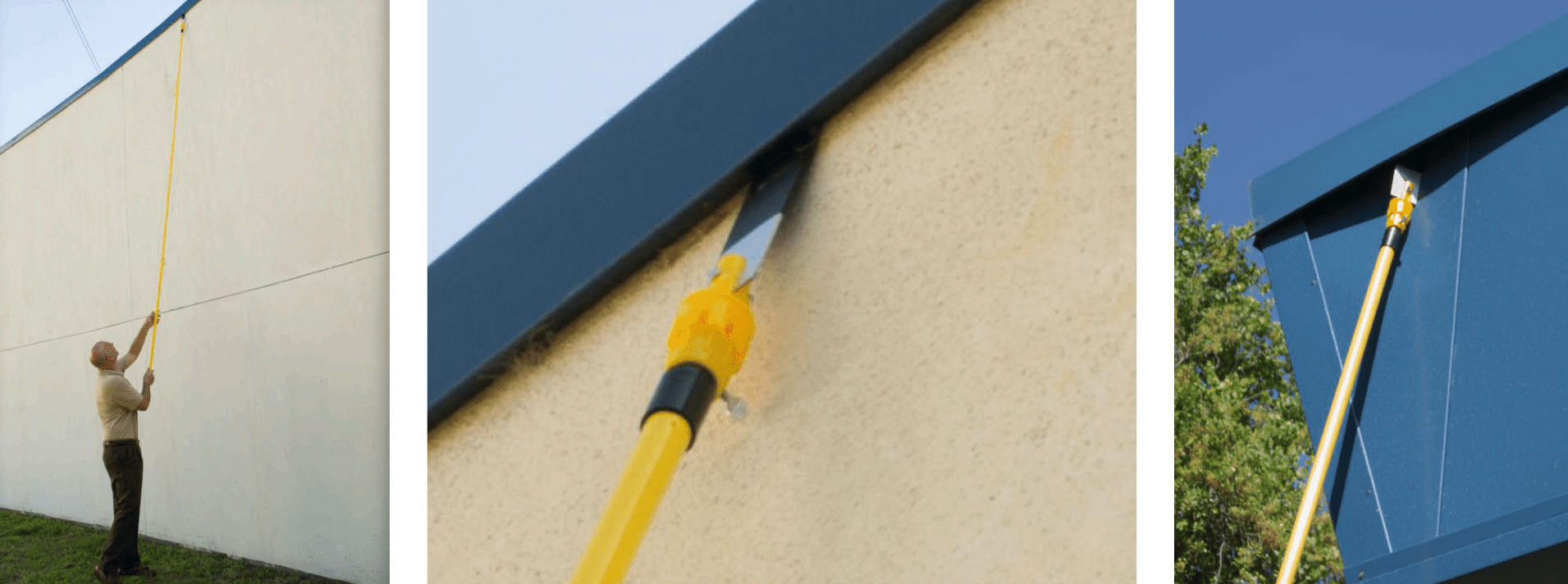
- Check for loose perimeter flashing. Loose or ill–fitted flashing greatly increases the potential for roof cover failure and water intrusion during high–wind events.
4
Roof–mounted equipment
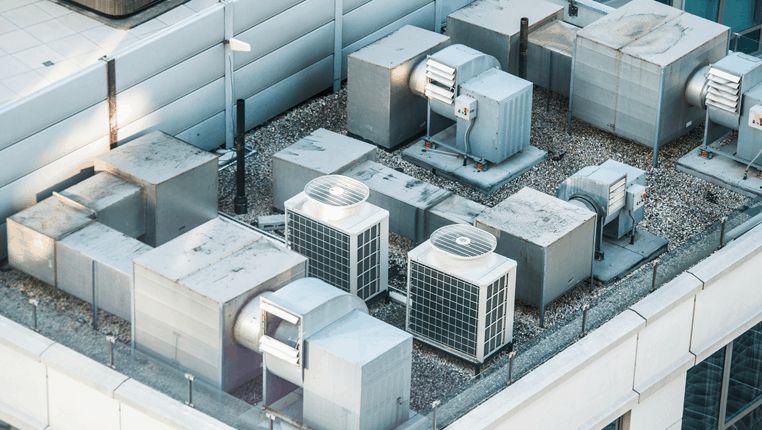
- Check equipment for rust on metal panels, screws, and metal flashing on curbs.
- Inspect equipment’s connection to the curb it sits on. Look for visible signs of curb leaks. If a water leak is suspected, check curbing for rot, and replace if needed.
- Pull on all cables and straps to verify they are tightly secured; there should be little to no slack. Check manufacturer guidelines for more specific information.
- Inspect for loose flashing around roof-mounted equipment curbs, which could lead to potential failures of the unit’s structure and water intrusion.
- Clear all debris around and under roof-mounted equipment. Debris can cause water to pond.
- Ensure service panels have all fasteners in place so panels do not become dislodged.
- After any service is performed on the roof, re-inspect equipment to make sure all screws, cables and straps are tightened and back in place and no debris is left behind.
- Ensure the blocks in a ballasted system are securely anchored to the tray and strapped or bolted together. Ballasted systems are NOT recommended in hurricane–prone regions.
5
Solar (photovoltaic) panels
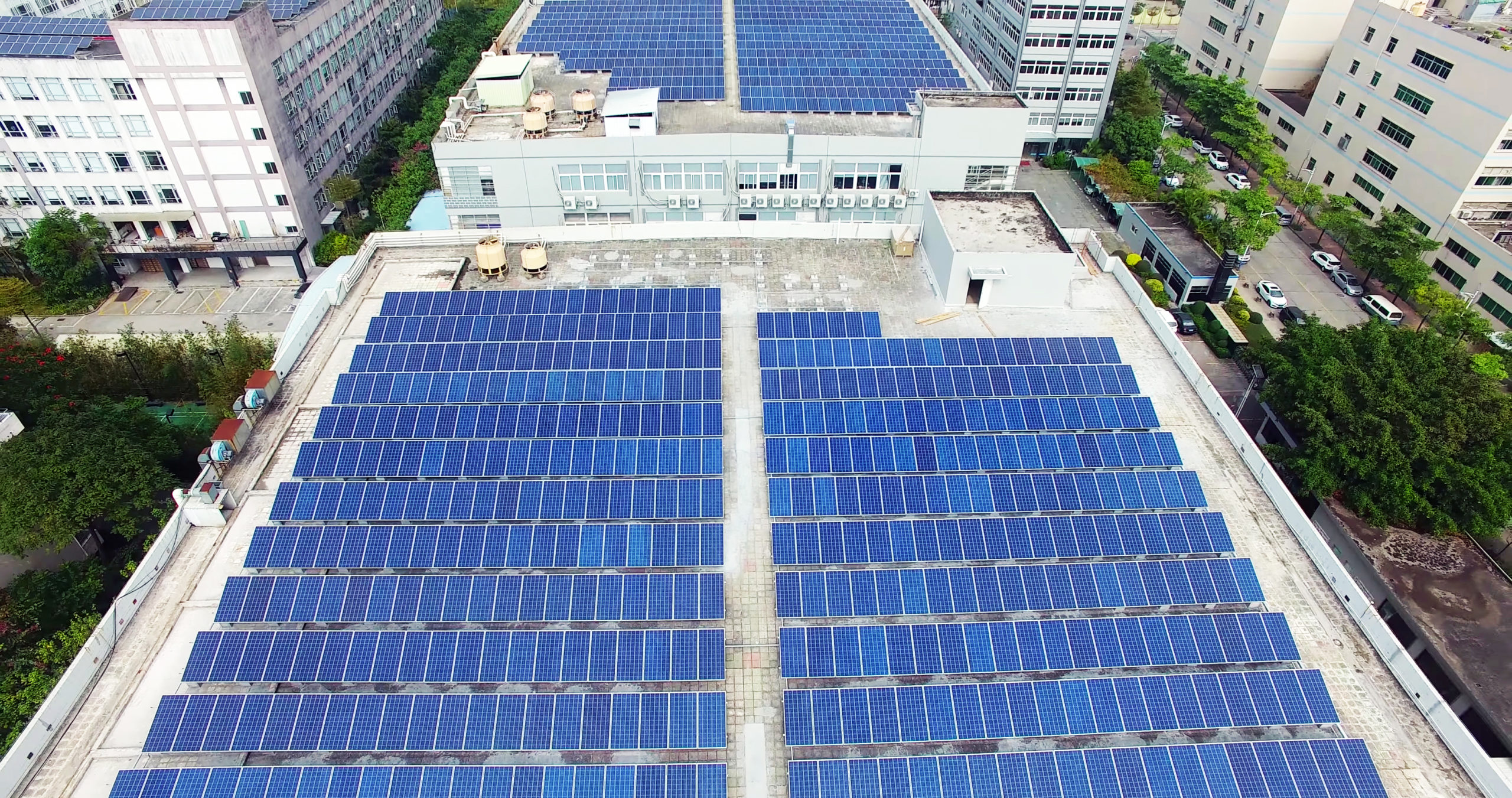
- Ensure the panels and hardware are secured properly. Ballasted solar panel array systems may slide or lift in high winds.
- Ensure the blocks in a ballasted system are securely anchored to the tray and strapped or bolted together.
- Ballasted systems are NOT recommended in hurricane–prone regions.
6
Lightning protection
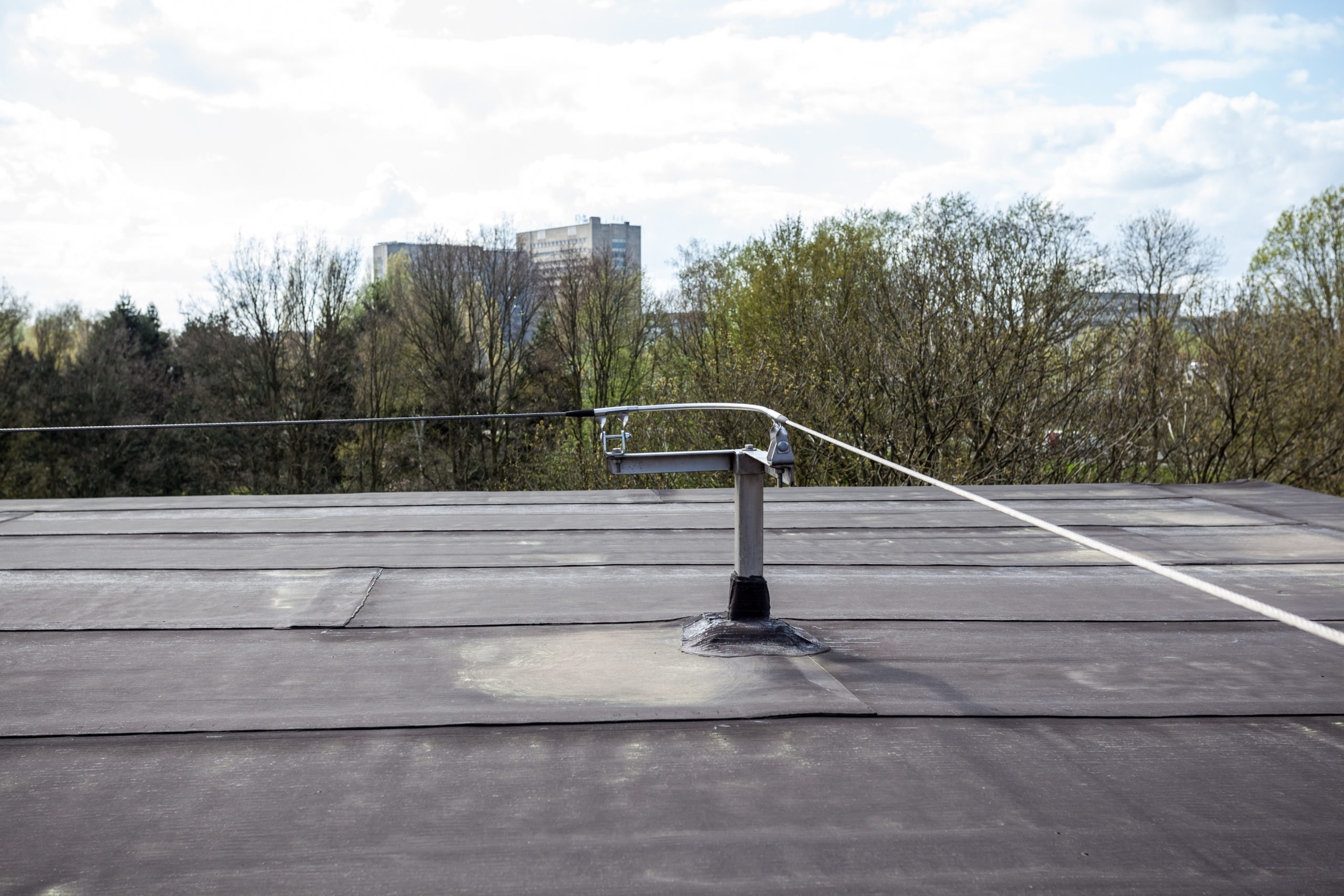
- Check to see if rods and cables are loose by gently pulling on the securements and conductor poles; there should be little to no slack.
- If replacement or a new cable connector is required, install a closed loop connector rather than a conventional 3-prong connector. If the metal conductor cable becomes loose from its securement, it can be dragged or slammed against the roof membrane causing damage.
7
Roof hatches
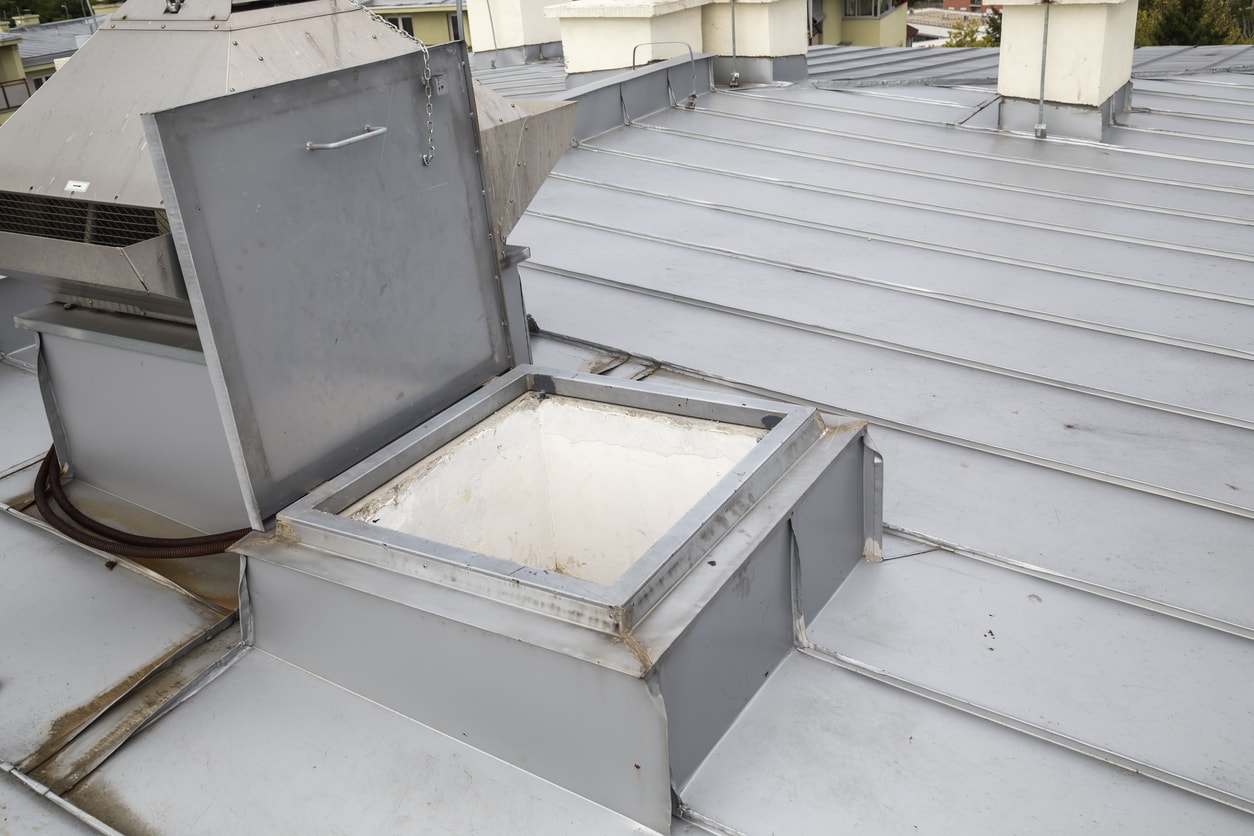
- Check roof hatches for any loose hardware (like bolts, nuts, or screws).
- Check flashing around the roof hatch for any cracks or leaks.
8
Skylights
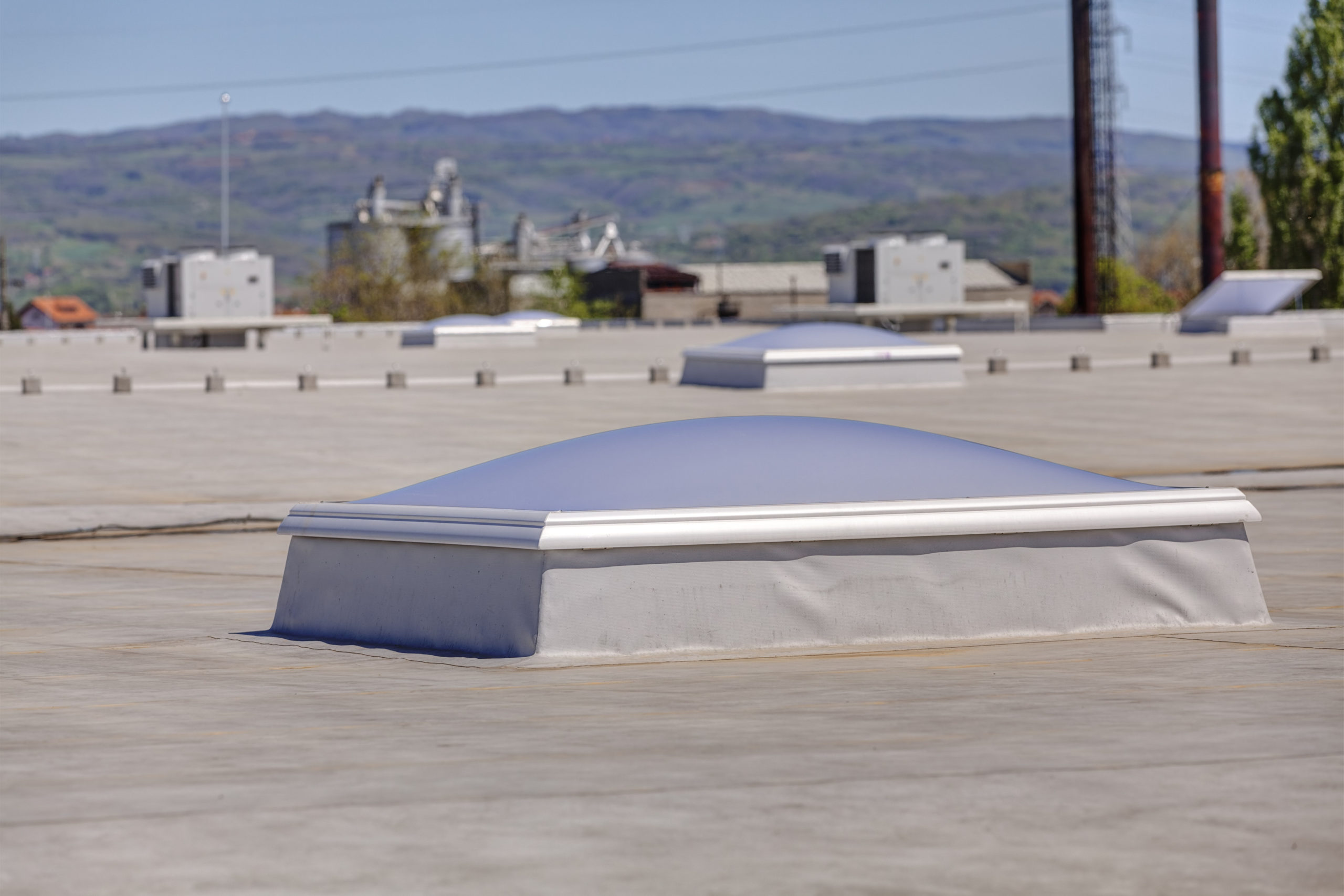
- Inspect skylights for cracks and leaks; also inspect securements to the curb around the skylight and address any rotting wood.
- Look for signs of hail damage.